Trailer Brake Failures: Top Mistakes We See in the Shop
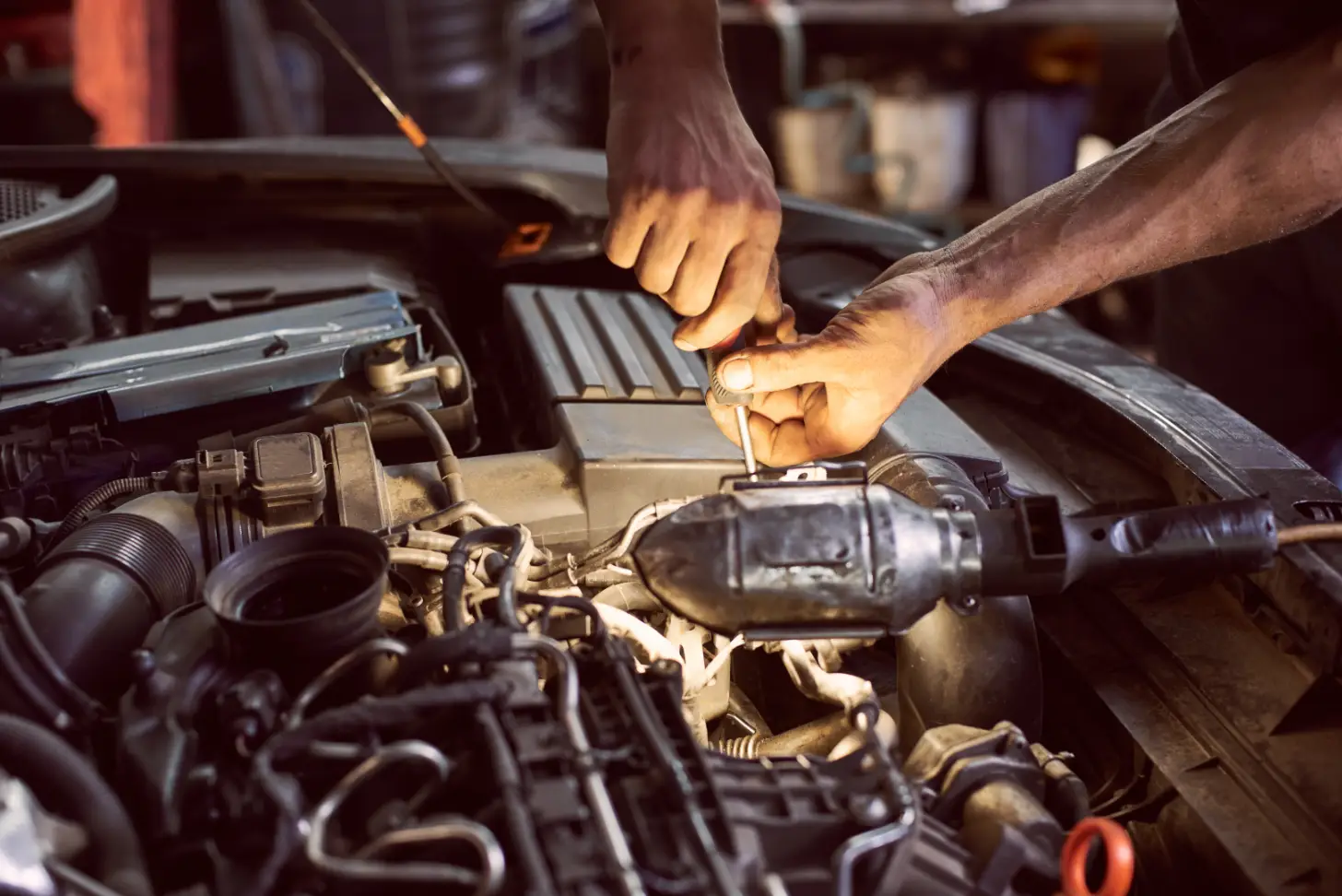
Common Mistake #1: Poor Slack Adjuster Maintenance
One of the most overlooked yet critical components in drum brake systems is the slack adjuster. This device not only transfers force from the pushrod to the S-cam, but it also compensates for brake shoe wear. When the slack adjuster isn't adjusted correctly—especially on manually adjusted types—it leads to an increased distance the pushrod must travel.
The result? Weak braking force or, worse, a complete failure to engage the brake shoes. A misadjusted slack adjuster is often the root cause of "long stroke" violations found during roadside inspections.
Practical Tip: For manual slack adjusters, perform routine checks every week. For automatic adjusters, remember they're not maintenance-free. If they’re out of spec, there’s likely an underlying mechanical issue.
Common Mistake #2: Neglected Air System Integrity
Every air brake system begins with the air compressor and depends on the integrity of the entire air delivery pathway. From air dryers to compressed air tanks and air lines, even a pinhole leak can lead to insufficient pressure.
Low pressure in the system prevents full engagement of the service chamber, resulting in partial braking. This isn’t just a performance issue—it’s a serious safety risk, especially under heavy loads or during emergency stops.
Practical Tip: Conduct a pressure leak-down test during PM inspections. Replace aged or brittle lines and regularly drain tanks to prevent moisture accumulation.
Common Mistake #3: Contaminated or Glazed Brake Shoes
Brake shoes work by creating friction against the brake drum. However, contamination from oil, grease, or even road grime can severely reduce this friction. Worse yet, repeated exposure to these contaminants leads to a glazing effect, rendering the shoes nearly useless.
Drivers often complain of reduced braking force, especially during long downhill stretches. This is a red flag for inspection.
Practical Tip: Always inspect for signs of oil or lubricant leaks from wheel seals. Replace contaminated shoes immediately rather than attempting to clean and reuse them.
Common Mistake #4: Ignoring Brake Drum Wear Limits
Every brake drum has a maximum wear limit—usually stamped directly on the drum itself. Exceeding this limit reduces the drum’s ability to dissipate heat and accommodate the brake shoe’s full range of motion. The result is both poor braking performance and the risk of cracking under load.
Practical Tip: Use a drum micrometer during service intervals. If you're nearing the wear limit, replace the drum. Don’t roll the dice on safety.
Common Mistake #5: Inconsistent Brake Balance
Brakes on a trailer need to work in harmony, not in isolation. A common issue arises when one axle brakes harder than another—often due to uneven slack adjuster settings, varied air line lengths, or differing service chamber sizes. This leads to uneven wear, poor stopping performance, and premature component failure.
Practical Tip: Always check brake timing using an applied stroke test. Uniform stroke lengths across axles are a good indicator of balance.
Common Mistake #6: Skipping Pre-Trip Inspections
Time is money, but skipping a five-minute brake check before hitting the road can lead to downtime that costs thousands. Drivers frequently overlook audible air leaks, disconnected air lines, or non-responsive brake chambers during walkarounds.
Practical Tip: Train drivers to look, listen, and test brakes during every pre-trip. It’s not just a recommendation—it’s a legal obligation under FMCSA regulations.
Common Mistake #7: Disregarding ABS System Faults
Most modern trailers come equipped with an ABS (Anti-lock Braking System). However, blinking or constantly illuminated ABS lights are often ignored. This is not just a compliance issue—it puts the entire braking system at risk during emergency maneuvers.
Practical Tip: ABS lights are diagnostic tools. If it’s on, it’s talking to you—don’t ignore it. Use a diagnostic reader to retrieve codes and address faults immediately.
Prioritize Brake Maintenance
Understanding the root causes of trailer brake failures is more than technical knowledge—it’s a matter of operational integrity and road safety. From slack adjuster misalignment to air system leaks and glazed shoes, the issues we see time and again in the shop are often preventable with disciplined maintenance practices.
If you require trailer maintenance in Richmond, VA, contact Dog House Trailer Repair today.